by
[user not found]
| Oct 08, 2014
Dust is deadly.
Since 1980, there have been more than 350 dust explosions that have killed more than 130 people in the United States alone.
Even the most safety-conscious operations can experience a dust explosion event. Grain milling and processing operations are at risk, as are food, wood and chemical processing plants.
Dust explosion prevention is a high priority. The National Fire Protection Agency publishes an annual guide to Combustible Dust that is an essential resource for all at-risk processing operations.
VIBCO Vibrators can be part of the solution. We offer ATEX and Explosion-Proof electric vibrators, as well as a full range of pneumatic and hydraulic vibrators for combustible dust environments.
Some key points to understand about combustible dust:
- What are dust explosions, and when do they occur?
- How to recognize dust hazards, and have good preparation and training in place, should an event occur.
- Where to find additional resources to help create a safer workplace.
What Are Dust Explosions? When Do They Occur?
A dust explosion is the rapid combustion of fine dust particles suspended in the air in an enclosed location.
The fine material can be any kind of material. Grain mill dust, saw dust, food ingredients including flour and powdered milk and even mined materials including coal and magnesium all have extensive records associated with workplace explosions.
The explosions are often very large, occur quickly and can be very destructive. In order for an explosion to occur, these 5 conditions must be met:
- fuel
- An ignition source and
- Oxygen
- Dispersion and
- A confined, closed off space
Industry experts have called these 5 components together the Explosion Pentagon (right)
Why and how is dust combustible? Some key characteristics are:
- Combustible by nature
- Dry - less than 25% moisture content
- Fine enough to go airborne
- Suspended in the air in an explosive concentration
- Contained or enclosed in a confined area
Dust explosions are unique in that they can occur in 2 phases, a primary and a secondary and spread quickly. The primary event is triggered when dust that has been settling on a surface for a prolonged period of time is suddenly disturbed. The dust becomes airborne in the confined space. When exposed to an ignition source - something as small as a spark discharged from a piece of clothing - the dust will ignite causing the primary explosion. The secondary explosion is often larger and more dangerous. The primary explosion can become an ignition source for a larger neighboring area, resulting in a much larger explosion.
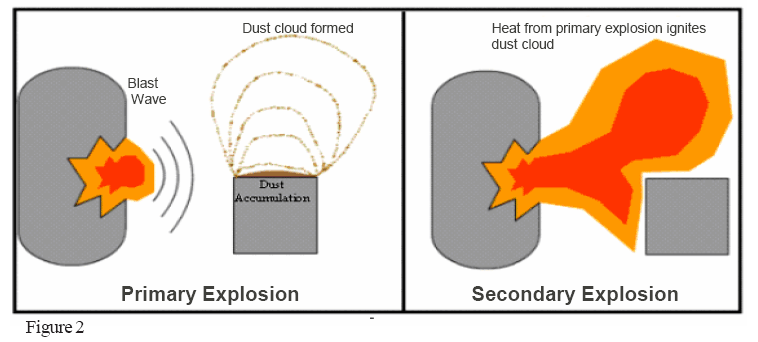
Ignition sources are many and varied - some obvious, some not. The Forest Industry Task Force found that mechanical sparks are the leading ignition source of dust explosions. After that, the second most common cause is 'unknown', a statistical slice that can range from random chance to a cause that was unseen or unnoticed. Beyond those two cases, everything from static electricity to friction to fire to hot surfaces are potential ignition sources.
Recognizing Dust Hazards, Preparation and Training
Grain Operations Safety is an important issue, and combustible dust explosions are a key part of that. Thousands of VIBCO vibrator users work in the feed and grain industry. We work to provide the best solutions for feed and grain to provide reliable, predictable and SAFE material flow and management.
All workers who are involved with milling and grain processing should be trained to identify risk-factors, mitigation procedures, and prevention/response to dust explosions.
Dust-heavy areas should have a ventilation system installed such as wall or ceiling fans that can provide additional air circulation and assist dust control and movement.
Hot Work Programs are special programs where work that generates heat or sparks are located in a designated area far away from floating dust or areas prone to explosion.
OSHA provides an comprehensive guide on how train your workforce to prevent dust explosions around grain.
Here are some of the points. Download the complete guide
- Maintain a rigorous housekeeping and sanitation program inside the grain elevator structure. Keep grain dust cleaned up in all working areas of the elevator
- Implement a weekly or bi-weekly bearing lubrication program based on the manufacturer's specifications
- Use a food grade mineral oil spray system on grain during transfer and load out
- Install bearing temperature monitors on leg boot, head and knee pulley shafts, on horizontal drag head and boot bearings and on belt conveyor drive and idler bearings
- Install belt rub sensors inside bucket elevator leg castings to detect belt misalignment to
- prevent friction heating.
Additionally, identify areas that produce dust and look for ways to isolate and/or contain that area from the rest of the working environment. This is especially crucial if this particular area is difficult to clean.
BE PREPARED! Make sure all your facilities are equipped with a fire extinguisher and other fire suppressing equipment.
Below are a few additional resources to consider: